Features of pad printing silicone 1. Good oiling and oiling effect 2. Fine glue, good resilience, and many times of pad printing 3. Clear pad printing pattern
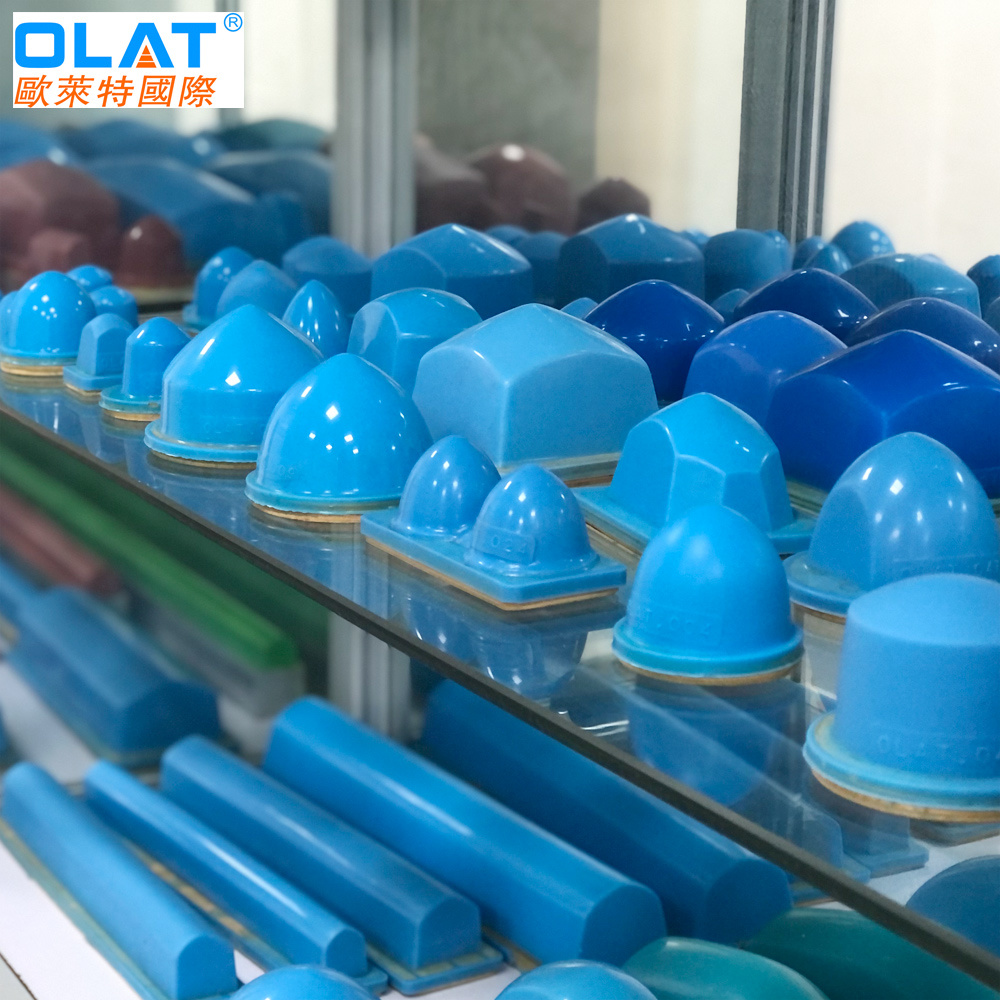
Edit this paragraph operation method - 1. First clean the mold with detergent, then dry or blow dry the water in the mold, and apply a layer of release agent. 2. The normal ratio of pad printing silicone and silicone oil is determined according to the customer's requirements. If the customer requires a large area of ??the printed pattern and a soft rubber head is required, more silicone oil is required. On the contrary, if the hardness of the rubber head is required, no or less silicone oil is added. Generally, the hardness of the pad printing rubber head is 15A~-25A°. If the amount of silicone oil is too large, the rubber head is too soft, and the number of printing times is limited. Yes, no matter how good the quality of silica gel is, its molecular weight will be destroyed by silicone oil, resulting in the phenomenon of wear resistance, solvent resistance and aging. 3. The general normal ratio is as follows: 100 grams of silica gel is added with 30 grams of silicone oil, and the hardness of the rubber head is 20A°, which is suitable for pad printing alloy cars and products with small patterns and small contact area. If the pressure contact surface is large or a soft rubber tip is required, the ratio of silicone to silicone oil can be 100:30, 100:50, but it should be noted that the larger the amount of silicone oil added, the softer the rubber tip, and the number of pad printing , wear resistance and solvent resistance will be reduced and reduced, and the number of pad printing products will be reduced accordingly, resulting in increased costs and waste of raw materials. 4. The amount of curing agent added and the chemical reaction of silica gel are as follows: Take 100 grams of silica gel and 50 grams of silicone oil, and then mix and stir. After the silicone oil and silica gel are fully stirred, add 2% of the total weight of silica gel and Add 3% curing agent, stir for 2-3 minutes, and then evacuate. The evacuation time is generally not more than 10 minutes. If the evacuation time is too long, the colloid will quickly solidify, which will affect the quality of the pouring glue. Edit this paragraph of the common problems of the pad printing pad 1. Why does the pad printing pad appear oily? The glue itself will not emit oil. It should be the compound of compound silicone oil and white mineral oil added during the operation. Because white mineral oil is a petrochemical product, not silicone oil, oil will appear. . 2. Why is the rubber head not durable? There are three reasons: a. There is a problem in itself. If the silica gel filtration time is not well filtered, there are impurities, or during the packaging process, the workers did not clean the barrels and tapes during the packaging process, resulting in the pad printing glue is not durable. b. It has something to do with the proportion of silica gel not being properly formulated, because the amount of silicone oil added has a lot to do with the amount of silica gel added. The more silicone oil is added, the softer the rubber head will be made. Durable and not wear-resistant, easy to age and other conditions. c. The manufacturer's reason, the manufacturer does not know how to use the pad printing pad, because the service life of the pad printing pad is closely related to the size of the printed pattern, if you want to print a larger pattern, you must use a large pad To pad printing, on the contrary, use a smaller glue head, and adjust the size of the glue head according to the size of the pattern (it is recommended that the ratio of the size of the glue head to the size of the pattern is 3:1). Why is the printed pattern unclear or incomplete? 1. The rubber head is too hard. If the rubber head is too hard, the printed pattern will be incomplete. Because the pattern pattern is too small and the glue head used is too hard, the glue head itself does not absorb the pattern ink on the steel plate on the glue head, so the pattern will be incomplete. 2. If there is moisture in the ink, the printed pattern will not be complete, and there will be spots and other conditions. It is recommended to clean the oil cup after get off work and replace it with a new one for water or ink. 4. Why does the pad printing head not drop oil? Because there are no painted plastic toys or products. 9 out of 10 During the process of pad printing, there will be a lot of release agent on the surface of 2 products. If the product has not been washed with water or face wash, clean it (remove the paint on the surface) and directly take it for pad printing There will be no oil drop. 5. Why is the pad not oiled during pad printing? Oil any glue tips or glue. If the customer prints a large pattern or a pattern with a thick font, it must be oiled during pad printing, but if the English letters are too small, the hardness of the rubber head is too large, and the ink on the steel plate is not adsorbed on the rubber head, so It won't get oiled. 6. Why is there moisture in the ink 1. The ink itself contains moisture, which has quality problems. 2. Because it is open when using ink, and in July, August, and September, the temperature of the weather is high, the water vapor will become water vapor when it encounters high temperature, and the moisture in the air will rise. The steel plate of the printing machine will form small water droplets, small water droplets, and small water droplets will slowly condense into large water droplets, which will flow to the oil cup. 7. Why do you need to add silicone oil when making pad printing silicone rubber? Because in the process of making pad printing silicone pad, when customers are printing products, the size of the pattern required by the customer is often changed, and the hardness of the rubber head also follows. and change. Adding silicone oil can dilute the viscosity of the silica gel and change the hardness of the silica gel. 8. Why does the pattern printed by pad printing have burrs or spots? 1. The rubber head is too flat, resulting in poor exhaust and poor resilience during printing. 2. The ratio of ink and Tianna water must be moderate. If the adjustment is not uniform and too much ink is added, pitting will appear. 3. It is recommended to clean the oil cup after get off work and replace it with new water or ink.

Instructions for use of pad printing silicone products: 1. First, clean the mold with detergent, then dry the water in the mold or dry it with an air gun, and apply a layer of release agent. 2. The normal ratio of pad printing silicone and silicone oil is determined according to the customer's requirements. If the customer requires a large area of ??the printed pattern and needs to use a soft rubber head, more silicone oil should be added. On the contrary, if the hardness of the rubber head is required, no or less silicone oil is added. Generally, the hardness of the pad printing rubber head is 15A~-25A°. If the amount of silicone oil is too large, the rubber head is too soft, and the number of printing times is limited. Yes, no matter how good the quality of silica gel is, its molecular weight will be destroyed by silicone oil, resulting in the phenomenon of wear resistance, solvent resistance and aging. 3. Introduction The general normal ratio is as follows: 100 grams of silica gel is added with 30 grams of silicone oil, and the hardness of the rubber head is 15A°, which is suitable for pad printing alloy cars and products with small patterns and small contact area. If the pressure contact surface is large or a soft rubber tip is required, the ratio of silicone to silicone oil can be 100:30, 100:50, but it should be noted that the larger the amount of silicone oil added, the softer the rubber tip, and the number of pad printing , wear resistance and solvent resistance will be reduced and reduced, and the number of pad printing products will be reduced accordingly, resulting in increased costs and waste of raw materials. 4. The amount of curing agent added and the chemical reaction of silica gel are as follows: Take 100 grams of silica gel and 50 grams of silicone oil, and then mix and stir. After the silicone oil and silica gel are fully stirred, add 2%- Add 3% curing agent, stir for 2-3 minutes, and then evacuate. The evacuation time is generally not more than 10 minutes. If the evacuation time is too long, the colloid will quickly solidify, which will affect the quality of the pouring glue.